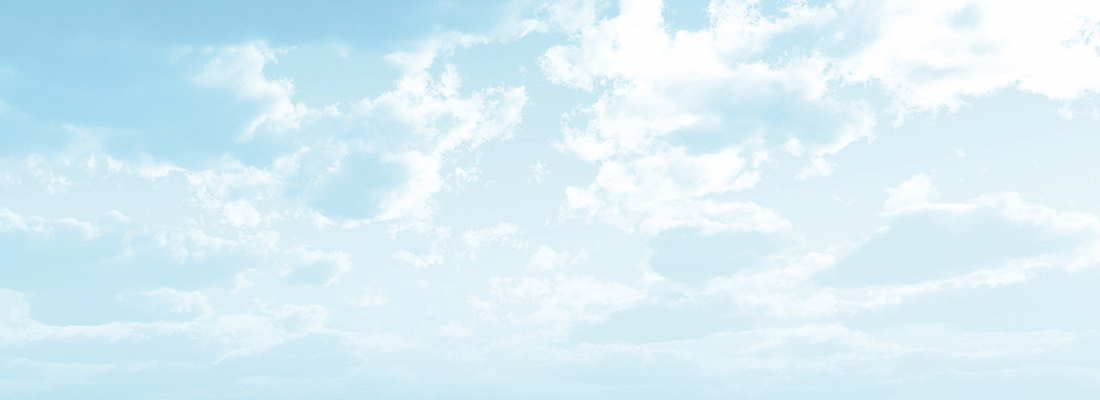
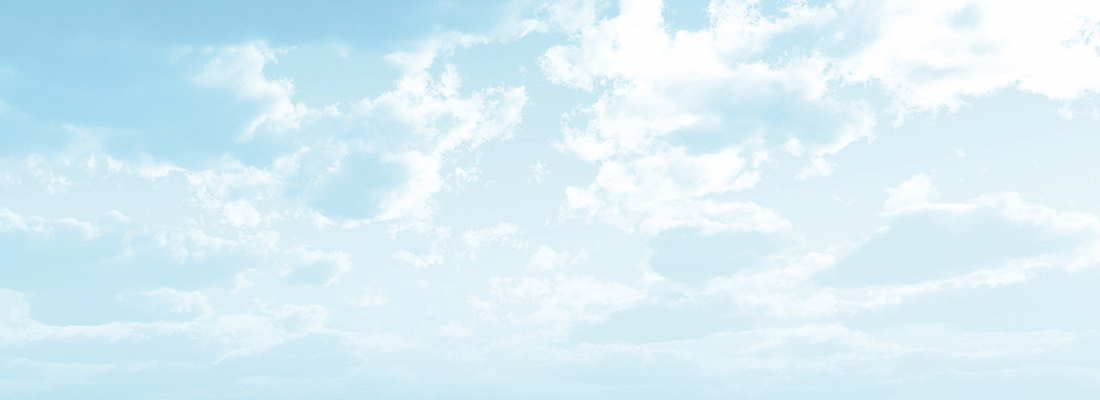
SACMI hero is a strategic and long-term project born in 2012. In a highly competitive market, such as the beverage one, Sacmi decided at that time to start brainstorming activities on how to combine Sacmi’s skills, know-how and technology portfolio giving our Customers added value in terms of product quality improvement, TCO reduction and minimal environmental impact.
Vertical integration of plastic processes and bottling is one of the key factors in creating added value for customers. heroPET4.0 is a patented technology that integrates in line and in a unique system 4 key processes:
-PET-drying, blending, feeding (plastic)
-In-line preform compression moulding (plastic)
-Bottle blowing (plastic)
-Filling and capping (bottling)
In addition, it offers the possibility to have 100% in-line quality control of preforms and bottles.
Looking at how the beverage business model has grown, from the beginning of the 1900s onwards, the starting point was an empty glass bottle transported to bottle filling lines.
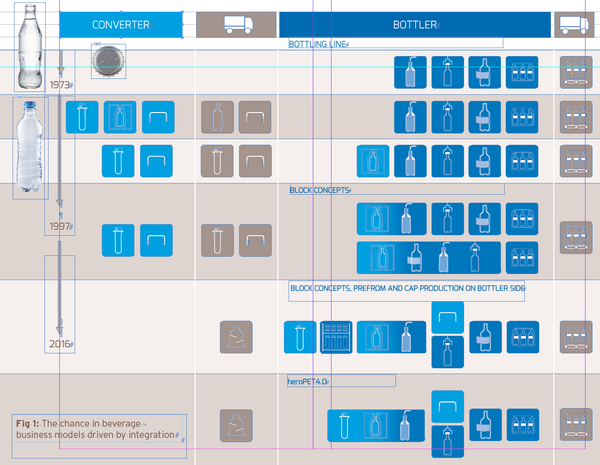
Fig 1: The chance in beverage business models driven by integration
When plastic bottles arrived on the market, the business model remained the same at the beginning (transportation of empty bottles and caps). But soon the blowing process was transferred to filling companies. The blowing machine was linked by air conveyors with the filler. The bottling process remained unchanged due to the need to wash bottles before filling, but an important step in logistic cost reduction was taken. When, 20 years ago, blowing integrated with filling/ capping appeared on the market, filling companies had an important improvement in the bottling process avoiding bottle washing before filling.
This first step in the direction of plastic processing integrated with bottling represents still today the latest significant innovation in the industry. According to Sacmi’s hero philosophy, the next step is represented by heroPET4.0: vertical integration of full compression preform production with blowing and filling processes (Fig. 1).
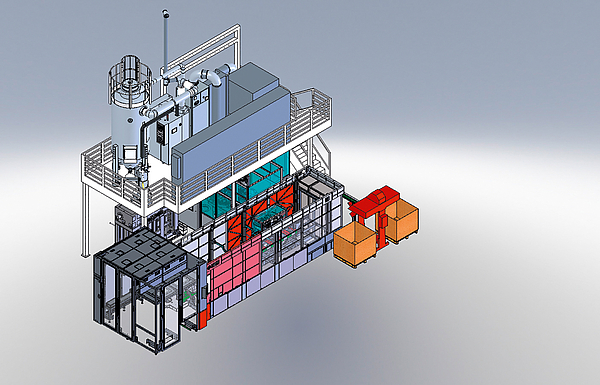
Fig 2: The preform compression moulding process is based on a rotary machine platform
The full compression moulding process is a well-known technology at Sacmi. As a matter of fact the company is the undisputed market leader in the technology of cap production by compression moulding. Following several years of development Sacmi is launching its ultimate compression technology for PET preforms. The preform compression moulding process is based on a rotary machine platform (Fig. 2), the ideal solution for continuous flow of orientated preforms. A synchronous preform handling unit feeds the warm preforms directly into the stretch-blow-moulding station (single stage).
Preform physical stability and properties are guaranteed by the innovative process integration management (Industry
4.0 driven), that features the most stable IV values and the lowest AA content.
Sacmi’s experience in plastic and filling was important and allowed us to identify and understand immediately the critical factors of integration of preform production within blow/fill. This is not easy and simple due to completely different requirements by the two processes. Preform production is characterized by: high efficiency (99%), 24 hours/day production, 7 days a week. Bottling figures are lower efficiency (90% typically), idle shift production during the week and seasonal production. The first key point of heroPET4.0 is flexibility. Since there is a difference in overall efficiency between moulding machines for preform and filling lines (starting from the blowmolder), in the case of filling line stoppage, the moulding machine for preforms automatically and instantly switches to cold preforms production which will be sent to an automatic ultraclean buffer system (Sacmi CPB). This flexible configuration of heroPET4.0 also allows production of cold preforms, just as a conventional injection moulding machine does, thus maintaining the advantageous and unique preform characteristics of the compression process. The stretch blowmoulding machine is in a standard configuration with a standard oven to grant the capability to heat and blow cold preforms. The second key point of heroPET4.0 is full compression moulding. Compression technology for preforms is based on a rotary machine platform, the ideal solution for continuous flow of orientated warm preforms. Neck handling assures no damage during synchronous transportation (Fig. 3).
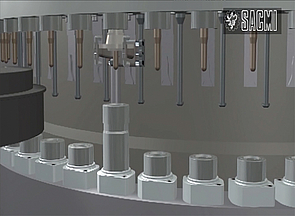
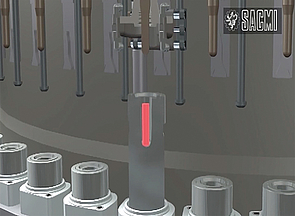
Fig 3: The moulding carousel: Cavity with PET gob inside is moving up to match the core and lips to have moulding compression preform transportation
Sacmi has been working on compression technology for PET preforms since 2002. Long development was significant also in building up skills in such technology and material handling. Many difficulties were encountered and trials carried out in order to achieve the final results of heroPET4.0. Sacmi invested heavily in these projects in terms of resources and finance (and also in patents) but never gave up in its determination to bring them to a successful conclusion because, following the strategy to reach heroPET4.0 level of integration, it is vital to have a simple, reliable, rotative, energy saving technology such as compression.
For filling companies, heroPET4.0 represents a solution that gives the following added values:
A. Quality improvement
A controlled and low contamination process (easy HACCP protocols) compared to the traditional way of stocking and transporting the preforms.
According to Sacmi’s experience in preform production and handling, the below chart explains how the preform contamination level usually evolves during standard preform production and handling, starting from the pellet state. It is evident that, no matter the original pellet contamination (usually from 100 CFU/g up to 100.000 CFU/g, according to pellet storage conditions), reaching melt status after extrusion, PET resin can be considered sterile due to the high temperature reached (270-280°C). Afterwards, due to traditional injection technology and traditional storage and transportation solutions, the contamination level increases. In the best scenario, preform contamination reaches a level of about 10.000 CFU/preform, similar to the pellet state before thermal treatment. In the worst case, if accidental contaminations occur, for example, from preforms touched by operators, octabin broken or tip over during transportation, this level can increase to a very high and unpredictable value. Finally, traditional methods for production and handling cannot guarantee either a low contamination level or repeatability. In such cases, contamination is defined not controlled. Sacmi heroPET4.0 makes it possible to keep the critical point where contamination of preforms could increase (HACCP) under control and then assure a lower final contamination level. Also, this contamination level can be considered repeatable (controlled contamination condition). This is true for both conditions of preform productions: warm preforms sent to blow/fill or cold preforms sent to a CPB buffer.
Laboratory results can confirm that general contamination in preforms (molds, yeasts and bacteria) coming out from heroPET is extremely low and at all times less than 100 CFU/preform. Then bottle blown contamination will be at the same level. The bottle contamination level guaranteed through heroPET4.0 allows filling companies savings on chemicals and cleaning operations especially for sensitive product filling lines (ultraclean, aseptic) (Fig. 4)
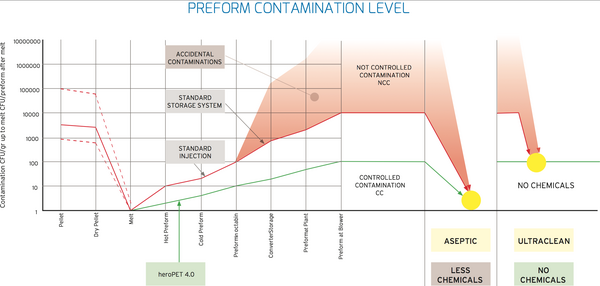
Fig 4: Preform contamination level
B. Energy and cost saving
The single stage process allows for energy savings up to 50% compared with the traditional double stage process, depending on preform thickness (Fig. 5).
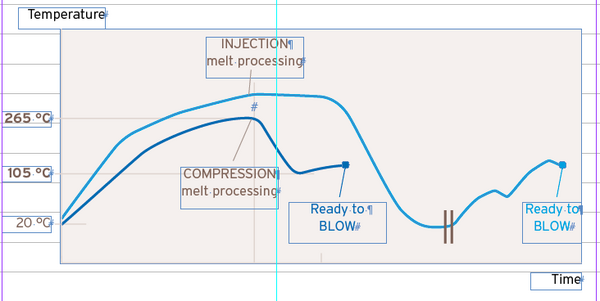
Fig 5: Energy saving
C. Material and cost saving
Compression technology makes it possible to produce ‘gate-free’ preforms. The absence of a gate reduces the preform weight from 0,2g to 0,4g, without influencing the bottle’s mechanical properties (Fig. 6). The preform base could also be optimized in weight thanks to the possibility to design a flat base (Fig. 7).
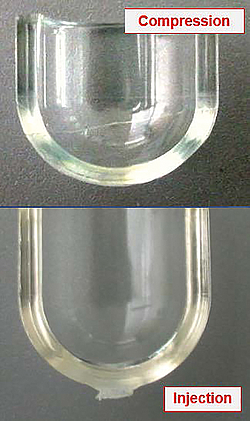
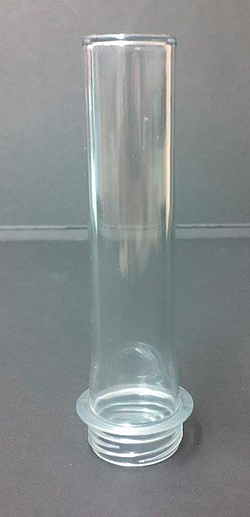
Fig 6+7: Gate-free and flat base prefrom design
D. LOW acetaldehyde
Low acetaldehyde content (lower PET melt temperature, lower residential time at max temperature, lower extrusion pressure). PET comes out from the extruder from a nozzle measuring between 10mm and 30mm. So PET resin does not have to move across hot runners, rotary joints and long channels. Shorter residential time and low pressure guarantee a minimum level of AA, and in any case lower than values obtained from standard double stage technology.
E. POSSIBILITY TO USE HIGH VISCOSITY PET
Possibility to use high viscosity PET (up to IV 1.15) having lower IV drop compared with the standard injection process.
F. HIGHER CONTAINER PERFORMANCES
heroPET4.0 allows the customer to save handling costs of preforms: such as costs for octabin or cages, forklift rent and maintenance, packing materials, costs for preform unscrambling and feeding equipment.
Sacmi ran an industrial validation test for one year. A strong development partnership was established between Sacmi and one of the biggest bottlers in Italy. Industrial validation was performed on a 0,5l bottle, still water, preform weight below 9 g. The heroPET4.0 system that was installed and validated includes a 48-cavity preform compression section and a 10-cavity blowmolding section for a production speed of up to 30.000 bottles per hour. Bottle contamination before filling is less than 100 CFU/bottle and these results confirm the quality improvement from a contamination point of view. From an energy saving point of view, heroPET4.0 consumes no more than 1 kWh/kg PET to have a blown bottle. This energy consumption also includes chilling (preform production and blowing process) and pump consumption. This is an overall consumption value. And we are just at the beginning. Wide margins of optimization are in the Sacmi development pipeline. In comparison with the most up-to-date double stage process, after many years of technological optimization, energy consumption of injection plus blowing for that preform/ bottle at that speed is in the region of 1,3-1,5 kWh/kg PET (excluding compressed air). From a bottle weight reduction stand point, heroPET4.0 technology makes it possible to reduce, as a first step, 4% of the total weight, keeping the same resin type, bottle shape and design, neck already used by the customer.
A base change to the flat shape will be one of next steps. Regarding acetaldehyde, the blocker has been removed since the beginning of heroPET4.0 production. As concerns intralogistics, heroPET4.0 leads to significant cost savings for preform handling.
For the preform of the above case study, the saving has been calculated to be in the region of 0,06 €/kg PET – 0,12 €/kg PET. Globally, integration of these processes allows filling companies to save on the total cost of the bottle a value between 5% and 15%.
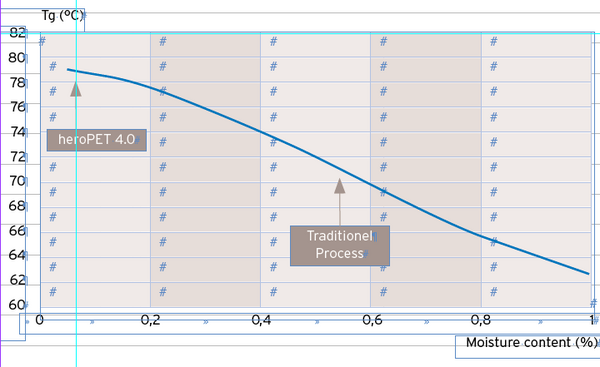
Fig 8: Moisture impact on PET transition temperature Tg
The comPETence center provides your organisation with a dynamic, cost effective way to promote your products and services.
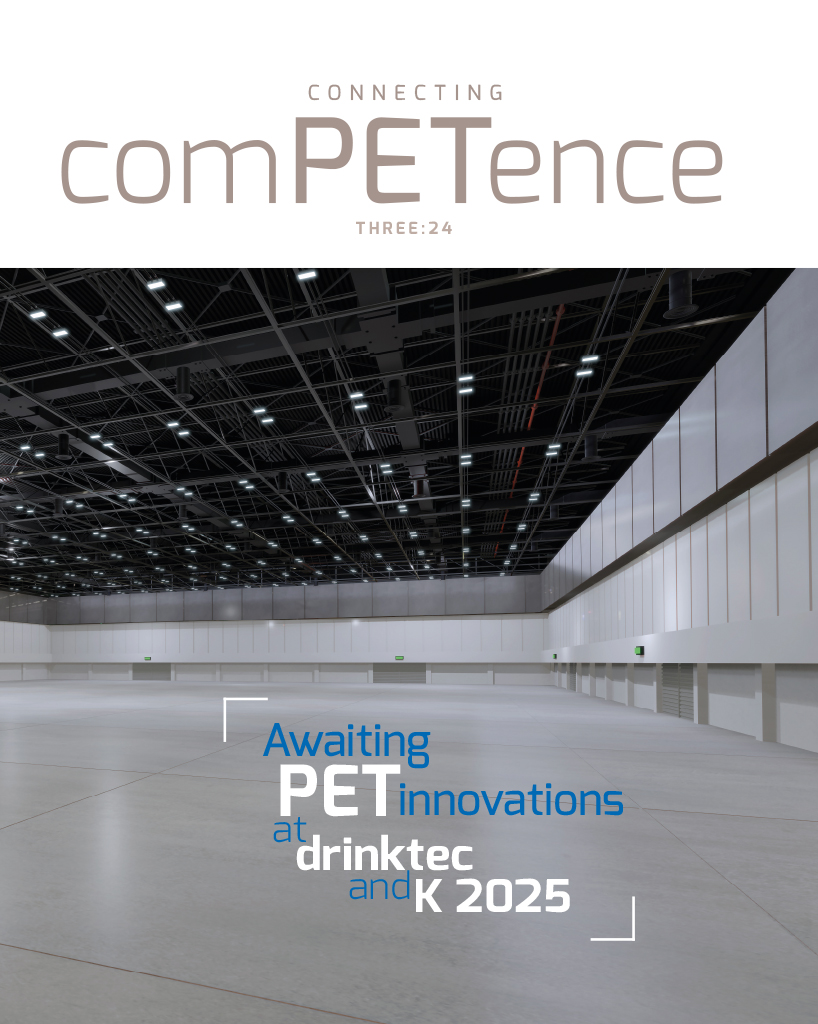
magazine
Find our premium articles, interviews, reports and more
in 3 issues in 2024.