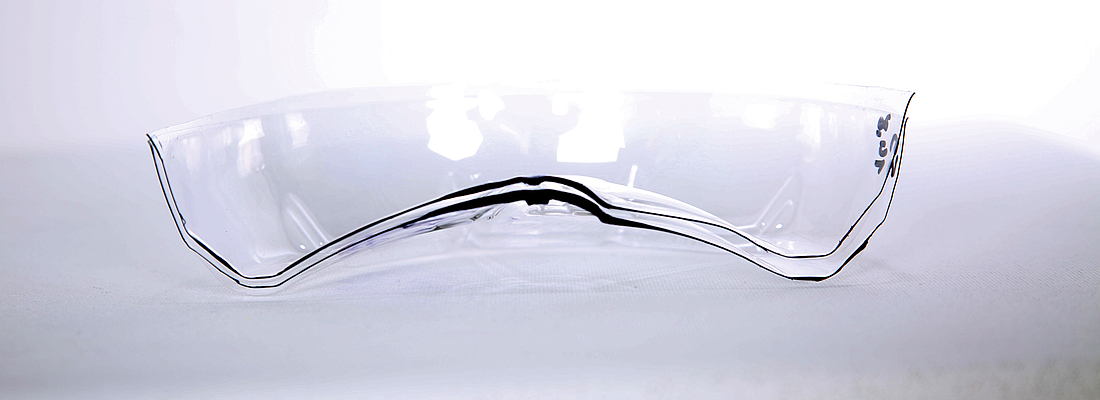
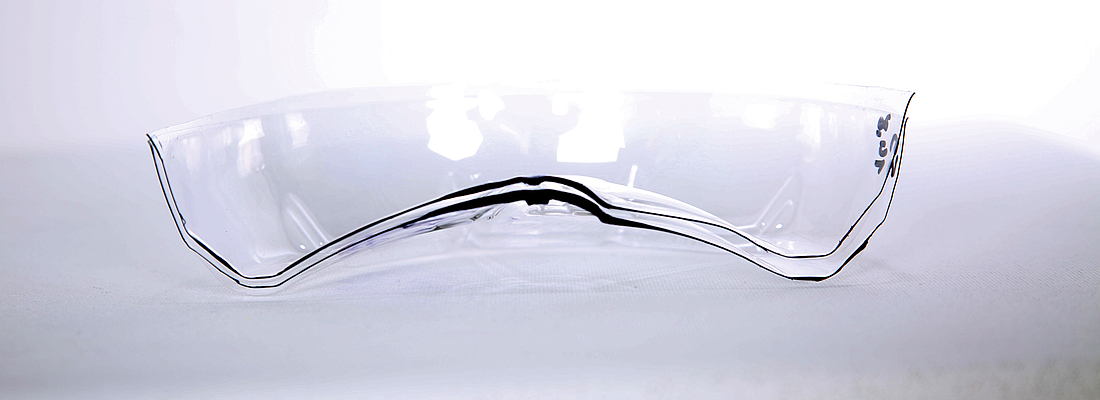
Lightweighting PET bottles is a process where we are continuously seeking and finding new potential. The quality of the bottles produced is strongly connected with this process as well as with bottle wall thickness, leaving us – in extreme cases – with a product that resembles a “capped pouch” that does not always keep its shape, causing it to collapse somewhat when opened.
Besides the body, there are also other parts of the PET bottle that have the potential to achieve significant savings without lowering the quality. It is a well-known fact amongst most converting companies that many PET containers carry large quantities of unneeded raw material, mainly in the base around the gate area. The savings potential depends on the container’s application. The total weight of small bottles could be reduced by up to 5%, and by up to 9% in bigger bottles from two to ten litres.
For many years, several companies have been focussing on finding a solution to the raw material in bottle bases and its cost-cutting potential. Most existing solutions in the world market change the base design of the preform into a conical shape, without considering the impact this has on the subsequent blow moulding process. Just one solution forms the base of the preform into a new shape using pressurised air, directly after injection moulding using the first heat. Even this technique has its limitations, because it only takes place on the outside surface of the preform, and the effect on the inside surface is varied and cannot be influenced. The end result is basically some sort of accident.
The above-mentioned issues gave Creative Packaging Solutions (CPS) the perfect platform and incentive to create Mint-Tec – an alternative solution to the processes that exist on the market today.
Mint-tec
Mint-Tec is also formed after injection moulding during the first heat. It does not use pressurised air, however. Our goal was to shape the preform from the outside as well as the inside. We do this by minting the preform base, realised by a special-shaped cooling sleeve in combination with a matching special-shaped minting head. These two shapes allow us to predict the exact shape of the preform base with 100% certainty depending on the raw material available in the former spherical base.
How does Mint-tec work?
-The preforms are produced using a standard injection moulding process.
-There is no need to change any main process parameters such as holding pressure, back pressure, temperatures and cooling time. Just a few small parameters need to be adapted. Mint-Tec enables spherical bases, conical bases and any other special designs to be minted.
-The take-out device receives the preforms from the injection mould.
-This device is equipped with specially designed cooling sleeves, which define the OUTSIDE shape of the preform base.
-The transfer plate is equipped with Mint-Tec units.
-The transfer plate now moves into the receiving position. Locking systems connect the take-out device with the transfer plate. Before the transfer is continued, the Mint-Tec units move inside the preforms to mint the final INSIDE and OUTSIDE design of the preform base under the specified force using Mint-Tec heads – a process with high repeatability.
-After the minting process, the Mint-Tec units on the transfer unit transfer the preforms to the conveyor belt or cooling bloc.
-The whole minting process takes place in parallel to the injection moulding process. Therefore, cycle time is not expected to increase. On the contrary, cycle times may be reduced thanks to the weight-optimised preform with thinner wall thickness.
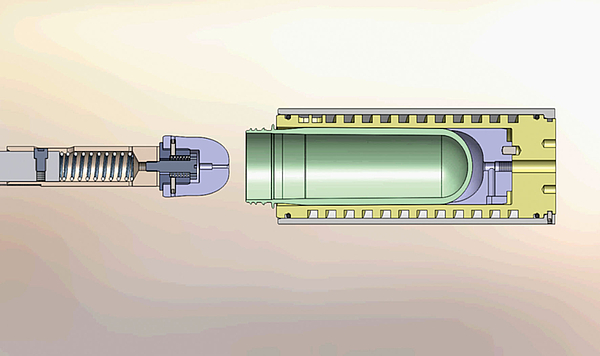
FIG. 2: Standard spherical base, Mint-Tec conical version, Mint-Tec ellipse version
How does Mint-Tec influence the blowing process?
Trial runs with world market leaders in blow moulding have proven that, in addition to all raw material savings, the energy and cycle time of the blow moulding process can also be significantly reduced:
-less energy needed for IR reheat because of higher preform surface and thinner base
-less blowing air pressure due to more optimally
distributed material
-less cycle time due to thinner base and therefore less cooling time
The following describes a 5 l/59 g/38 mm/twist-off neck sample from a customer project:
Figure 2: Standard spherical base, Mint-Tec conical version, Mint-Tec ellipse version
Figure 3: Minting unit with a base cut 5 l preform
Figure 4: Base cut 5 l bottle, Mint-Tec version shown above; standard version shown below
Our customer tested two different versions of Mint-Tec design. The first one was a conical version and the second one was an ellipse version. After different blowing tests the decision was taken to continue with the Mint-Tec ellipse version due to the better process window in the following blow molding process.
The results after blowing with Mint-Tec ellipse version (see figure 4) are as follows:
-saving of 4.0 g per bottle totalling 6.7%
-injection moulding machine, 72 cavity, cycle time 15.0 sec,
yearly production 8,200 h
-saving of raw material: 566 MT/year
-Total saving: 622,600 euros/year (calculated with a resin price of 1,100 euros/ MT)
What is the roi?
Example: 5 l container/59 g preform
Investment to be made:
-Trial run depending on the product and requirements
-Take-out device, together with special Mint-Tec cooling sleeves
-Transfer plate with implemented Mint-Tec units and locking system
-Cooling block with special Mint-Tec cooling sleeves depending on the machine
-If there is an existing mould, a new set of cores is needed to reduce the weight
-ROI for 72 minting heads: less than six months (the ROI does not take into account the savings from the blow moulding process)
Mint-Tec offers customers the possibility to produce thick-walled preforms with a thin-walled preform base and an increased surface for the blow moulder’s IR heater. Mint-Tec is compatible with almost all customary preform systems, including Husky, Netstal, Sipa, Sacmi and Sumitomo systems. With the exception of core changes, existing moulds do not need to be modified if the aim is to reduce weight. The take-out device and transfer plate of the preform production system need to be replaced due to the new base shape. However, for a new investment, the end customer only needs to make additional investments in Mint-Tec units and some technical robotic adaptations.
What are the customer’s benefits in numbers?
CPS can roughly estimate the savings in material by analysing the bottle to be optimised. To evaluate the exact savings potential, the final properties of the bottle must be defined and a trial run carried out before any investment is made.
Thanks to this new approach, CPS is now able to offer a solution to save raw material in the bottle base of any application and to optimise the bottle base with regards to a perfect wall thickness distribution.
conclusion
The Mint-Tec innovation gives the freedom of bottle design back to the blow moulders. Bottlers are now free to design their special bottle bases without being limited by the preform design. For the first time in the PET industry, blow moulders can define their exact wishes for an ideal preform. This will lead to new bottle and preform developments for the future of PET.
Meet Mahir Aktas at PETnology Europe 2015,
Nuremberg/Germany, 09-10 November, 2015
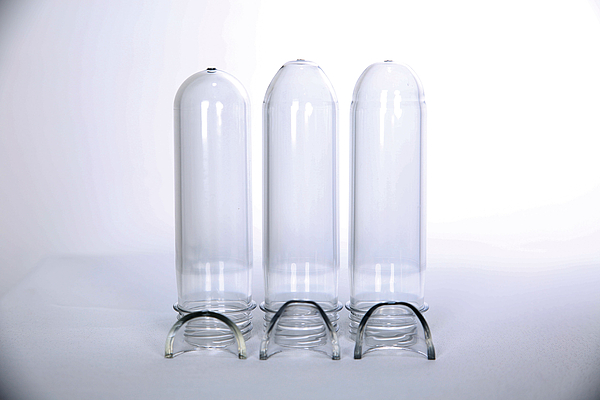
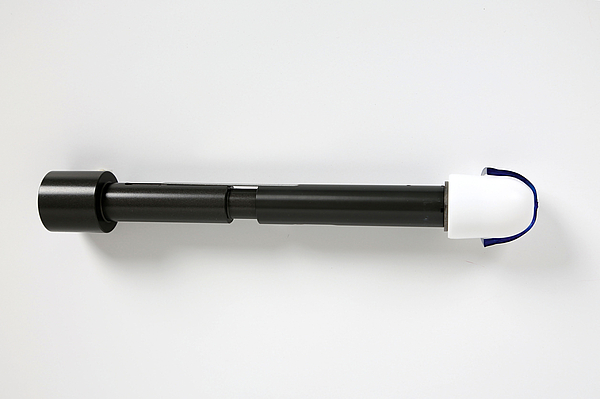
FIG. 3: Minting unit with a base cut 5 l preform
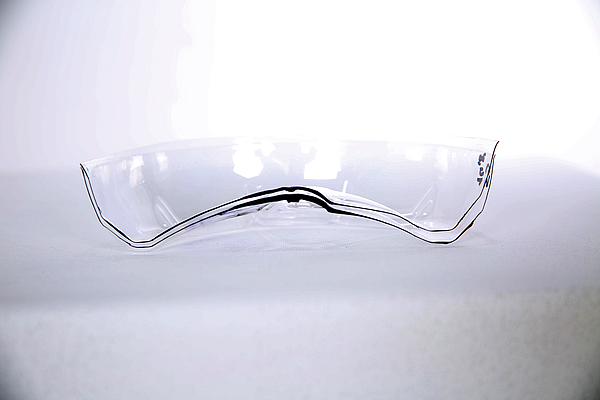
FIG. 4: Base Cut 5L bottle, top Mint-Tec Version, below Standard Version
The comPETence center provides your organisation with a dynamic, cost effective way to promote your products and services.
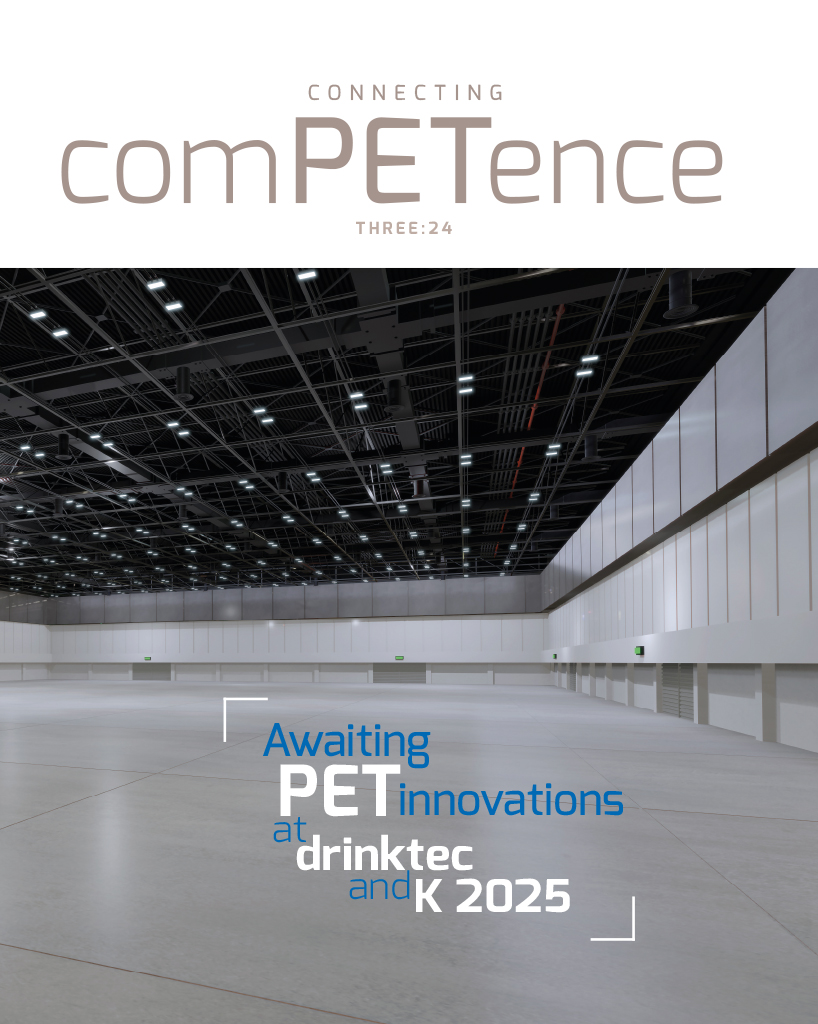
magazine
Find our premium articles, interviews, reports and more
in 3 issues in 2024.