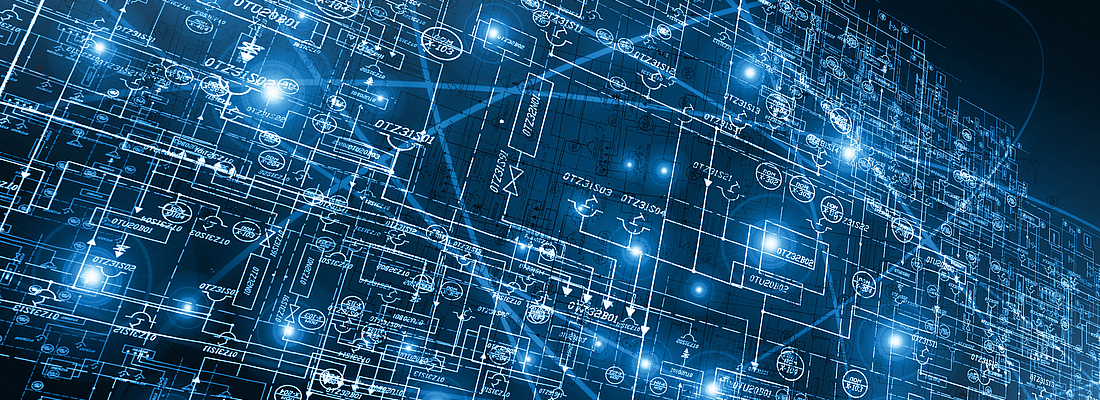
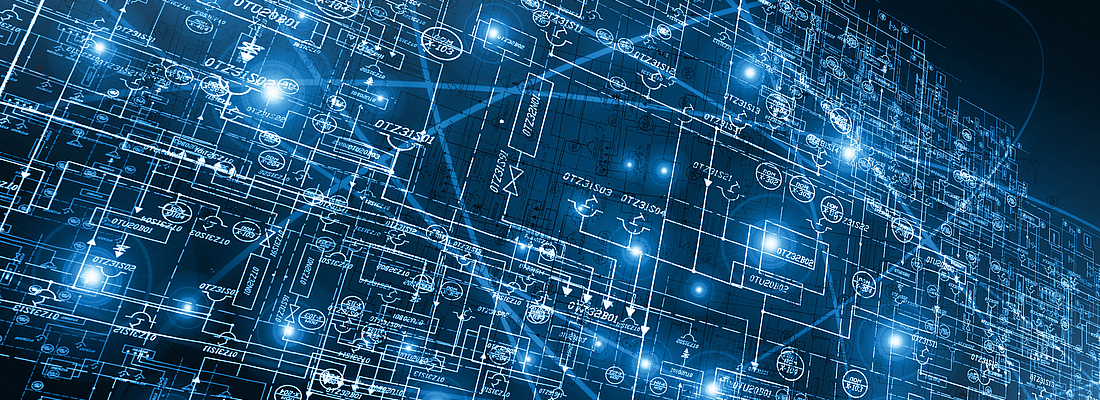
Industry 4.0 (i.FOUR.ONE) is one of those topics that every production company will have to face. Is it just media hype or could smart phones, smart homes, smart cities, smart mobility and smart factories really usher in a new era of production?
On a recent flight from Frankfurt back to Munich, I sat next to a young man who I thought looked like a business studies student or a young consultant. As it turned out, he had been working for a renowned international consultancy for a year. After studying international business and management in London and Madrid, he completed a Master’s degree in Paris. Everything went very quickly. “Everything happens very quickly nowadays,” the somewhat restless, eloquent young man says, holding an iPhone in each hand. Working? Oh yes, he has been working a lot, often late into the night. “Or should I say the early hours of the morning?” What is falling by the wayside, he wondered. And so did I ...
What effect do social media, and the internet in general, have on his industry and his working life? What area was he currently working on exactly? “Industry 4.0 – in general. That’s all I can say!” There we were, sat next to each other, probably both thinking about 4.0 whenever the conversation stopped. And I realised that I had been asking myself these questions for a long time: What can the PET packaging and filling industry expect from these new developments? Who is working on them and how much progress have they made?
Digitalisation is a profound key word that changes our work, our processes, our companies and our lives. Everyone is talking about the fourth industrial revolution, although the first three were only recognised as such in hindsight. This is not the case anymore – today we are well aware that something is coming, if we are not already in the middle of it.
DIGITALISATION
As early as in 2006, a debate on digitalisation was started in the USA under the heading of Cyber Physical Systems (CPS) – a debate that did not reach Germany until 2011, where it was known as Industry 4.0. Speed and time are particularly relevant factors in the digital world, which is reflected by the fact that five years are the equivalent of almost an entire generation in digital terms.
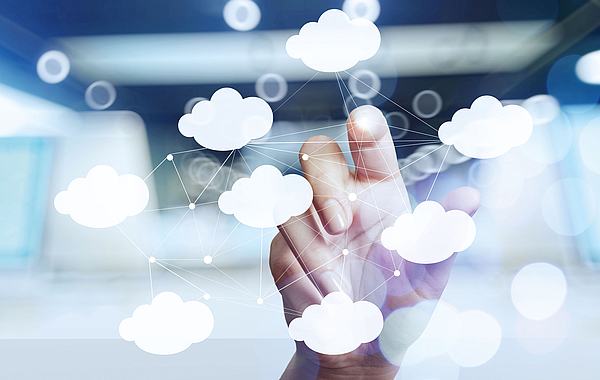
SPEED AND DATA VOLUME
Speed is no longer an issue in PET stretch blow moulding technology! Or is it?
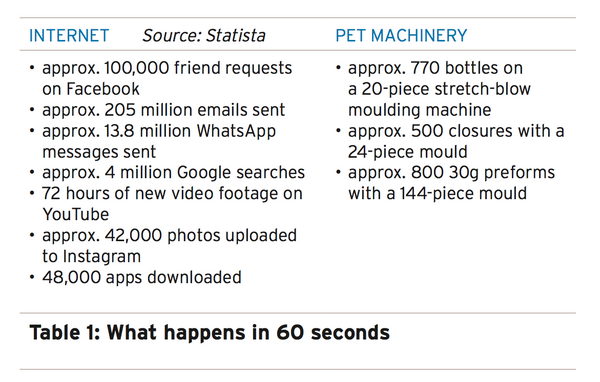
I suddenly start thinking about my son: When he was about three years old, he collected snails and put them in a bucket. By the time he had gone and collected more from the field, some of his captives had already climbed back out. “They’re so fast!” he said, crouching in front of the bucket.
Speed – is it just in the eye of the beholder at a given time? Snails have not become noticeably faster over the last 20 years.
Will the internet of things “only” revolutionise assembly processes after CIM (computer integrated manufacturing) and lean manufacturing, or will it revolutionise entire business processes and models? Is it just media hype or could smart phones, smart homes, smart cities, smart mobility and smart factories really usher in a new era of production and filling for PET packaging? Will machines now be digitally connected, or “blocked”, as per the mechanical block method? Will we soon be talking about “smart packaging”, or even “connected packaging”? Or perhaps the development of Industry 4.0 will fail to penetrate the factory gates of PET processing, filling and packaging? To me, it seems naive to believe this if we look at numerous examples from other industries.
INDUSTRY 4.0 IN THE SPOTLIGHT
The first industrial revolution began with the invention of the steam engine in around 1750. Industrialisation became possible, and steam and work engines markedly improved logistics with steam boats and railway lines, as well as boosted agricultural productivity and thus basic supplies.
The second industrial revolution was shaped by the division of labour and mass production, which became possible by inventions such as the conveyor belt developed by Henry Ford, and electrical energy. Electric drives allowed a shift away from centralised power machines and towards decentralised, electrical drive systems.
The third industrial revolution started in the 1960s, when electronics and – a little later – information and communications technology came along. These technologies formed the basis of automation, which led to rationalisation and simultaneous series production of a wealth of variants.
All of these technical changes have transformed our social, commercial and industrial lives – and created winners and losers.
Industry 4.0 is one of those topics that every production company will have to face. Industry 4.0 has an effect on the operational framework of the performance process from procurement and production to sales and recycling. Globalisation and – above all – individualisation are becoming ever more important.
We have often seen world market leaders respond to changes too late, not feeling the pressure to make changes until it is too late, missing the signs, or not wanting to see or take them seriously.
THE DIFFICULTY OF DESTROYING
YOUR OWN BUSINESS MODEL
In the past, when we took holidays snapshots, the film was exposed (polyester) and then placed in a plastic tube to protect it from light. Upon our return, we would take the film to be developed and wait for an entire week before being able to “relive” our experiences and share them with friends.
Today, our smartphones take photos and videos that can be sent around the world within a fraction of a second (see table 1). Photos are sent in immense numbers, often without the recipient actually asking to see them – all thanks to digitalisation and the internet.
We all know of established companies and products, from the floppy disk to the mobile phone industry, that found it difficult to maintain their leading position. Flash memories, for example, were inferior to hard disks in terms of capacity, reliability and price for many years, which is why hard disks continued to be integrated into PCs. Flash memories do have the advantage of being small and energy-efficient, however, which is why they are now used in new fields of application, such as USB sticks, digital cameras and MP3 players, and now even replace traditional hard disks in laptops. Their great success in these new markets has triggered two developments that work in favour of this disruptive technology (see disruption on the right): Sales figures for flash memories are rocketing, which is causing prices to drop, and the memories are being improved continuously.
New companies with innovative products and new business models tend to change the established “rules of the game”, and are suddenly able to produce or offer products and services at much cheaper prices. In the past, quantum leaps were frequently made as the result of new materials and automation, changing, and even transforming, machines, processes and markets. Today, it is digitalisation and networks that are driving forward development.
When companies change, jobs change. You could say that jobs are shifting more than ever towards the requirement of better qualifications and, above all, boosted levels of creativity – at least at this stage in the digitalisation era.
Digitalisation affects individuals, companies and workplaces. In other words, society as a whole, irrespective of class, group or industry. This fact is referred to as “disruption”, which describes the transformation and destruction effected by digitalisation.
If current headlines and publications are anything to go by, disruption transforms, or even destroys, almost everything in its path: the music industry, the publishing industry, the photography industry, retail...
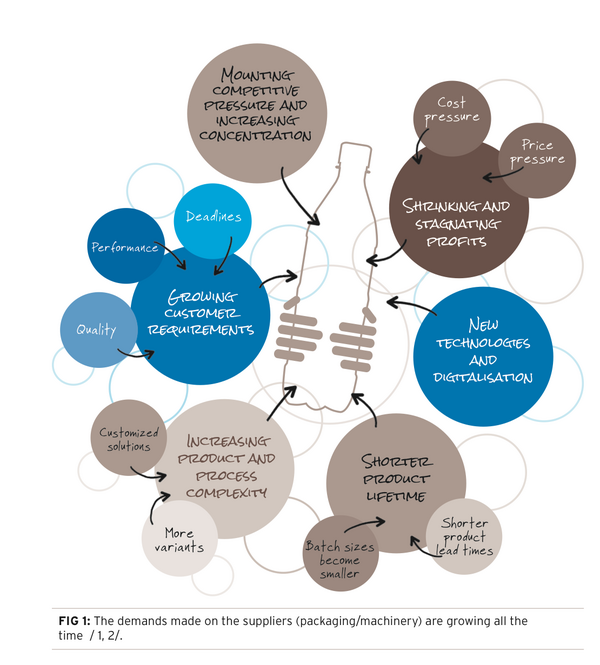
WHAT CAN THE PACKAGING AND FILLING INDUSTRY EXPECT, OR WHAT SITUATION IS IT ALREADY IN?
The rising number of economic operators in the PET packaging market coupled with growing expectations has made competition considerably fiercer for PET packaging and PET machine manufacturers in recent years (FIG. 1) / 1/.
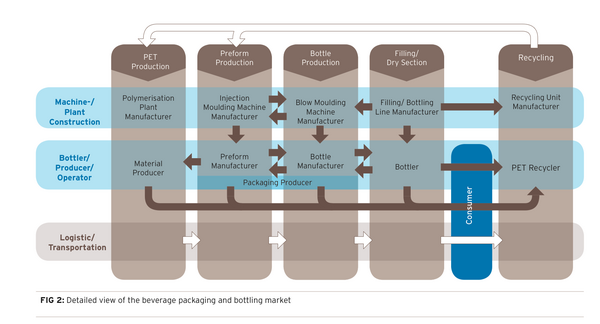
Every step towards gaining control of other parts of the value-added chain leads companies away from their core competences, the goal being to expand these competences in order to exploit synergies, simplify business processes and improve profitability. There is a rise in complexity, however – in terms of both the market and the reliability required of products and machines.
In the production sector, we can observe fillers crowding into the domain of converters. Fillers are producing more and more of their own PET bottles, increasingly taking the first steps towards their own preform production. Converters, on the other hand, are moving into the field of recycling and considering taking over responsibility for filling through wall-to-wall concepts. These are just some of many examples.
Understanding fast-growing and changing markets will become more and more important in order to gear products and – even more importantly – services towards global market and rising individualisation.
This can only be achieved by companies that – based on their business plan – recognise potential developments in the main influential factors and integrate their conclusions into their strategy.
Developments and changes in the market now necessitate continuous monitoring of operational performance processes, also with the help of digitalisation, in order to survive in the market.
In the past, the only way in which this could be profitable was by coming up with a new, better product. In the future, this won’t be enough – with regards to both machine and plant engineering and PET packaging itself.
So what are the next steps towards optimisation, and who has to take them?
To make production even more efficient and – above all – more flexible, machines and products should communicate with each other in the style of a social network. Factories and production will be intelligent and connected. Machines will become cyber physical systems with sensors, actuators and small embedded computers, able to organise production automatically, probably beyond corporate borders.
Systems for quality assurance and process control in particular are certain to present innovations in the near future which will help to meet the demands of the digital world.
What gets measured gets done
How far is the producing and filling industry away from developing an autonomous factory? The arrival of internet technologies and the subsequent connection of machines (M2M) is underway. M2M is all about monitoring, controlling and documenting processes. The IPv6 internet protocol has paved the way for the internet of things, where every object could theoretically have its own IP address.
But it is about much more than just equipping machines with IP addresses. It concerns the merging of production and company IT systems, the synchronisation of industrial processes, and the ability for machines to make real-time decisions autonomously.
Equipment that can organise itself is at the centre of digitalisation. At its heart are mechatronic production units, objects, devices, modes of transport, logistics components and buildings – the cyber physical systems (CPS) mentioned earlier. These systems can communicate over the internet and use online services. CPS can directly perceive their environment thanks to sensors, evaluate this information with available data, and influence the physical world using actuators. An evolution that is moving from vision to reality step by step: smart factory.
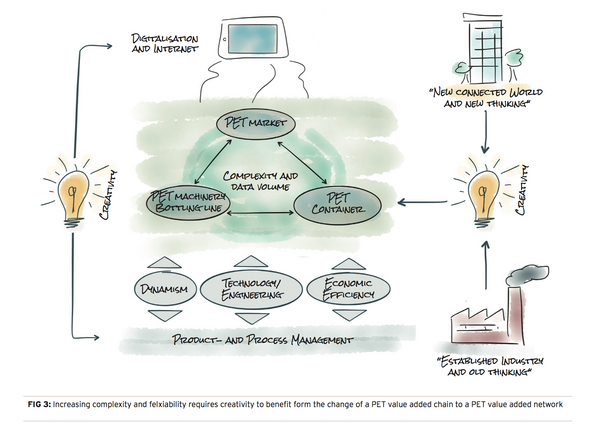
Customised solutions have created a much larger number of variants, which poses as much of a challenge to machinery manufacturers as higher quality demands and shorter delivery times.
To meet the growing demands on suppliers in the PET industry, an innovation spiral has been set in motion, considerably boosting productivity and reducing energy consumption in preform and bottle production in recent years, and may now be close to reaching its limits.
Machine manufacturers are still being forced to help their customers cut production costs further by offering innovative developments.
Looking at the value-added chain in the production and filling of a PET bottle, it soon becomes clear that market participants are not just trying to come up with new innovations in order to assert their position, but are also expanding their activities in the neighbouring elements of the value-added chain (FIG. 2). This process set in a few years ago, leading to the formation of larger companies and thus to concentration and a market limit.
INCREASING COMPLEXITIES
The German and European machine and plant engineering sector for the packaging and filling industries relies on exports. The excellent innovative performance of this established industry in recent years has ensured its export strength and continues to do so. Is this the way it will stay in the age of the internet within this digital world? Will mechanics lose its importance?
I never did find out what exactly that young man I met on the plane was working on. But it doesn’t really make a difference, anyway. All of our trains of thought could run on parallel trajectories – Industry 4.0 is effective in all sectors. Everywhere, similar questions will have to be asked, and similar methods will be used to find the right answers.
From the PET value-added chain to the PET value-added network
This first contribution in a series of articles on digitalisation, the internet of things and Industry 4.0 in the new comPETence magazine aims to create a framework and platform for presenting and discussing the challenges, changes, opportunities and risks for all players along the PET value-added chain.
The comPETence center provides your organisation with a dynamic, cost effective way to promote your products and services.
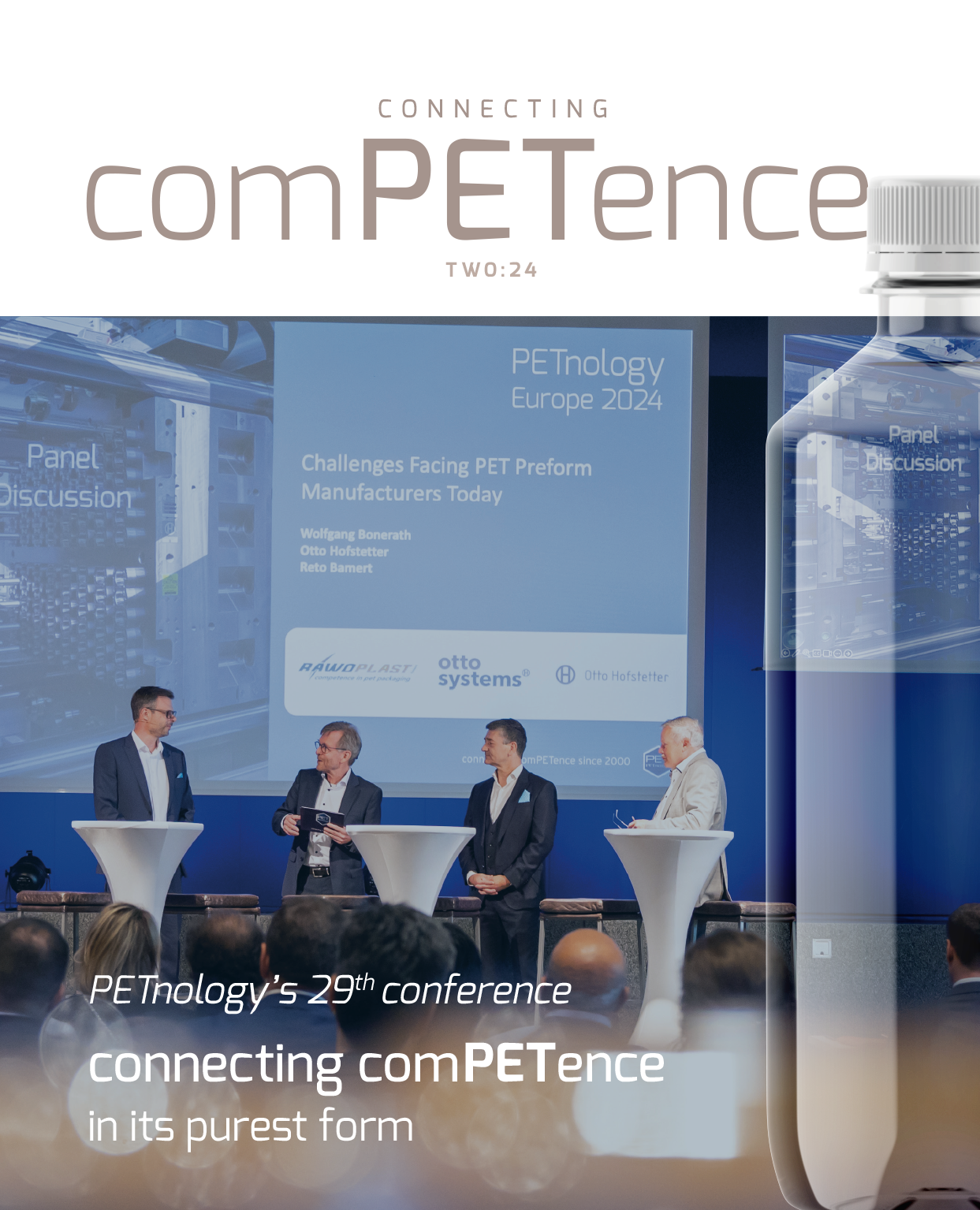
magazine
Find our premium articles, interviews, reports and more
in 3 issues in 2024.