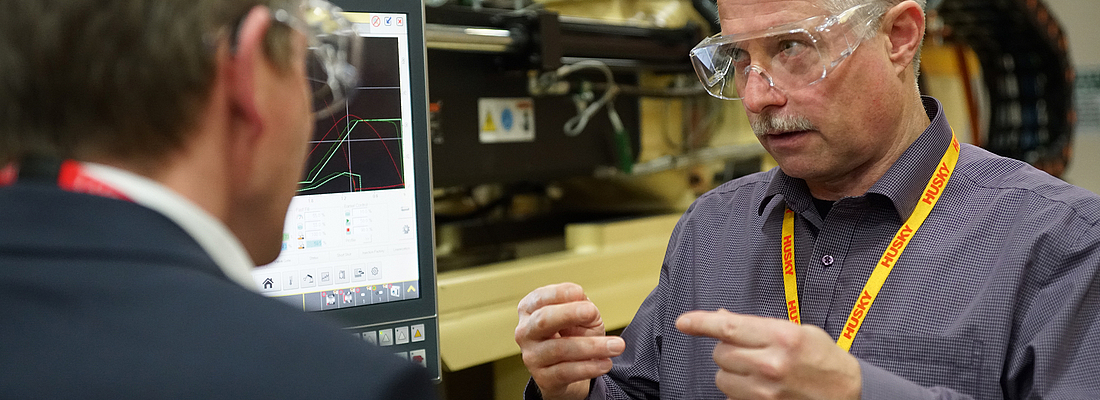
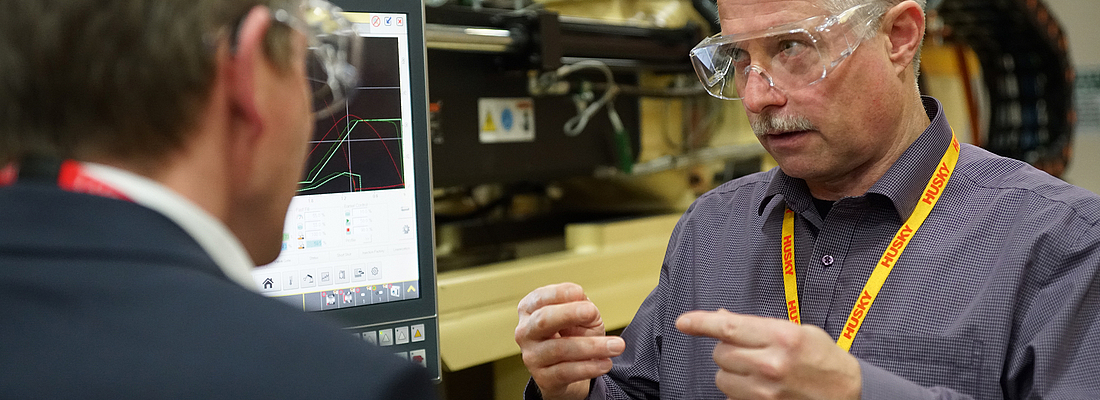
A tour of the HUSKY AdvancedManufacturing Center (AMC) with Joachim Niewels, Director of Husky‘s global Advanced Solutioning Team.
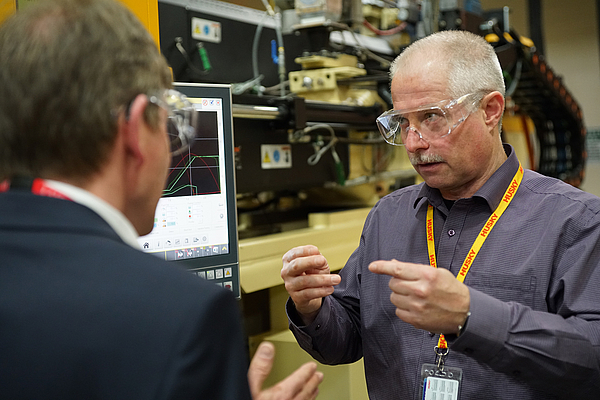
At the beginning of the tour we agree, the basicrequirements for injection moulding are covered. Thereduction of costs remains a central factor, but newvalues are emerging: the future lies in the creation ofadded value.
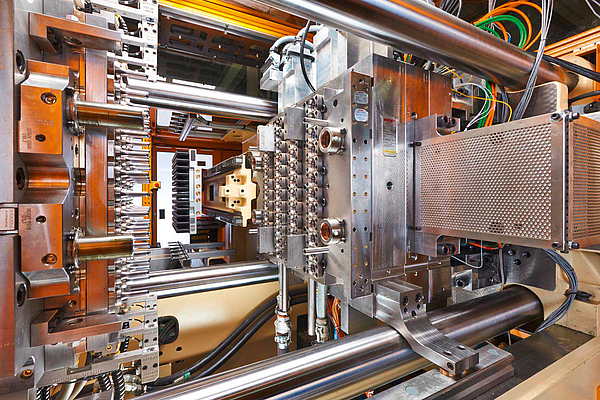
The AMC is dedicated to developmentsat HUSKY. Here, developments andideas are tested under productionconditions. Advanced Solutioningcombines translating customers unmetneeds into new technology solutions.“The most interesting cases for usare when we have the opportunityto anticipate and translate not yetarticulated manufacturing needs intotangible solutions,” says Niewels. “Todo this, we need scientific insight anda deep understanding of the processesinvolved.”
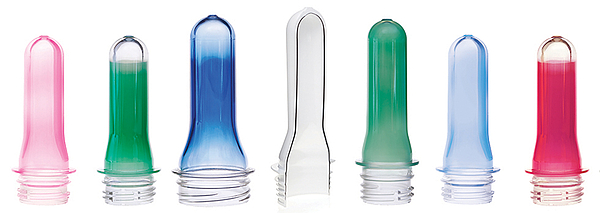
Recognising and implementing customerneeds: This approach will take systemsand their technologies to the next level.The technical maturity of basic functionsopens up new space for optimization andinnovation centered around integrationof production processes.Here, it is evident that digitisationis beginning to take hold: Machinesare getting smarter. A first step andprerequisite for this is the developmentand integration of new sensors. Oneexample that Husky has developed is asensor for measuring “mould breathing”.Originally designed to ensure perfectmould alignment, these sensors haveevolved into a valuable processing toolfor optimising the injection profile.In the future, more functions thathave been traditionally performed byoperators will be integrated into systemfunctionalities. In short, machinesare becoming smarter. Hypotheticallyspeaking, this means that the machinecould send a signal to indicate “I amnot feeling well” while at the same timemaking suggestions to alleviate theproblem. This is made possible by theskill ful application of new sensors thathelp to gain a deeper understanding ofthe process.Niewels explains: “Integration iscontinuous. To put it simply: customerswill be less interested in intricatetechnicalities and more focused on keyvalue drivers like capability, cost, quality,and availability.
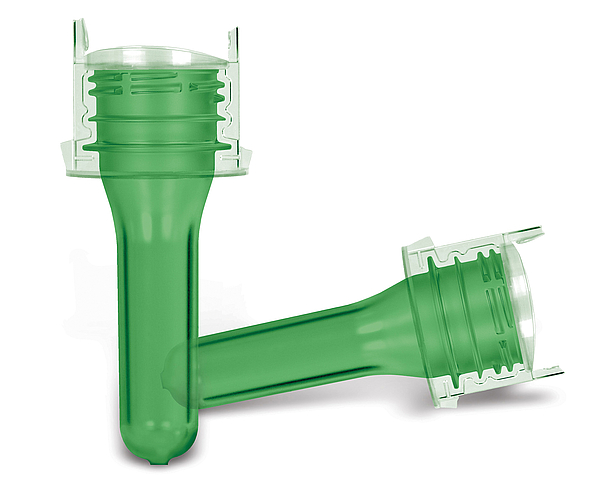
During the tour, we focused on threetopics:
MULTI-LAYER TECHNOLOGY
The industry has been concerned withbarriers and product protection for quitesome time. Ultimately, the aim is to openup new areas of application.“Based on the experience we gainedfrom developing our High PerformancePackage (HPP) and in particular ourability to precisely control the meltfront, we decided it was time to explorenew avenues in multi-layer technology,”says Niewels. Today, Husky systems arecapable of running cycle times of lessthan 5s with a 144-cavity mould. “Thisspeed requires highly dynamic andprecise melt front and melt flow control,which had been previously unavailable.Our technicians were extremely eager toincorporate this capability into the multilayerprocess, to reassess and evolvethis process to a new level of capability.”“Our multi-layer technology opens upa large range of possibilities in packagedesign.” It is no longer just aboutbarriers. The underlying technologiesare expanding the range of availableapplications. “We have established anextensive range of options. And ourcustomers are always coming up withnew ideas for colours or novel materials,as well as requesting new characteristics,which can have built-in time functions,”continues Niewels. Using a multipositionvalve checking system, Husky’ssystems are now able to shift the layersinwards or outwards. The complexity ofthe relationships between temperatures,viscosities, and other factors requireshighly dynamic, precise melt frontcontrol in order, for example, to usethe barrier material as economically aspossible. Niewels comments: “With anintegrated system, it becomes possibleto precisely measure the layers, bringingcontrol to new levels.”
SELF-CLEANING MOULDS
“With the development of self-cleaningmoulds, we have created an additionalbenefit – and reacted in advanceto a need which had not yet beenarticulated,” says Niewels, describingthe added value. Self-cleaning at the press of a button: Manufacturers are saved costlydowntime and operators no longer have to undergothe unpleasant and difficult process of manualcleaning with dry ice. But self-cleaning moulds alsocreate added value in situations where the customeris working under time pressure and might forgonecessary cleaning procedures, thereby running therisk that the job cannot be successfully completed.
HyCAP4
HyCAP4 is HUSKY’s state-of-the-art product systemfor injection molding beverage closures. Energyreduction and cycle optimisation are at the forefrontof this development and serve to increase theproductivity for closure manufacturing.HyCAP4’s waterfall concept is a primeexample of the possibilities that emergefrom integrating intelligent solutions. “Inthis case, it is a matter of optimising theejection curves of the closures to reducethe mould lock time,” says Niewels, whoalso sees this as an example of the newcontrol level in the injection moulding ofclosures. The ejection arcs of individualparts are optimised with the aim ofminimising the mould opening width,in order to reduce the time needed toopen and close the mould. This is easilyachieved through simple touchscreen commands on the system’s integrated19-inch operating panel. The systemthen automatically takes over the actualoptimisation and sets the relevantparameters.To close, we ask ourselves, wheredo we stand in the product life cycleof mature PET preform injectionmoulding technology? And whichfactors distinguish competing systemsuppliers from one another? Could itbe this “new level of integrated systemfunctions”, that will ultimately make allthe difference in the current competitiveenvironment? We will keep you up todate with the latest developments.
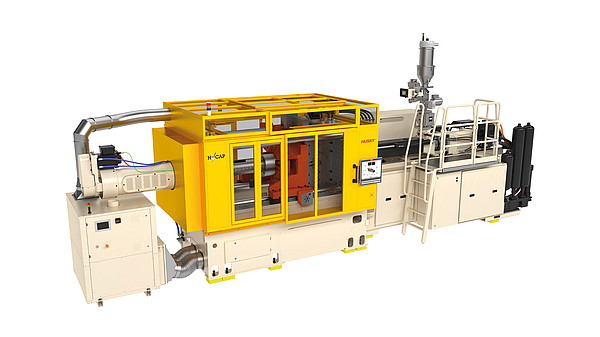
The comPETence center provides your organisation with a dynamic, cost effective way to promote your products and services.
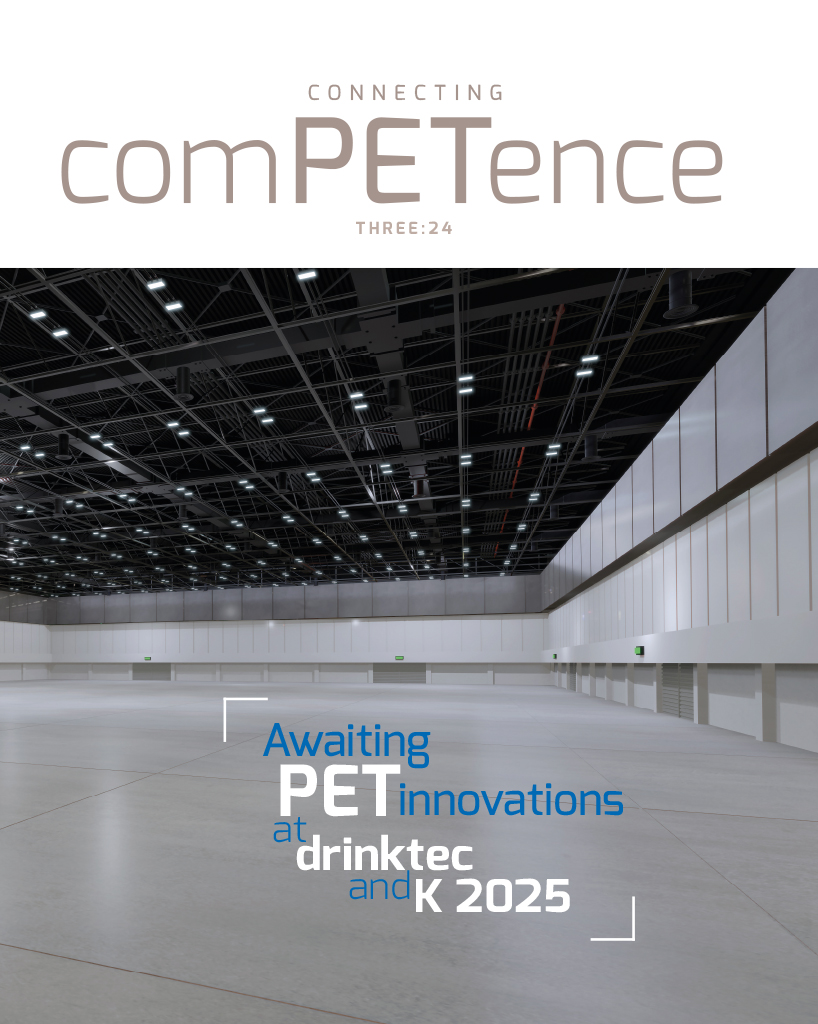
magazine
Find our premium articles, interviews, reports and more
in 3 issues in 2024.