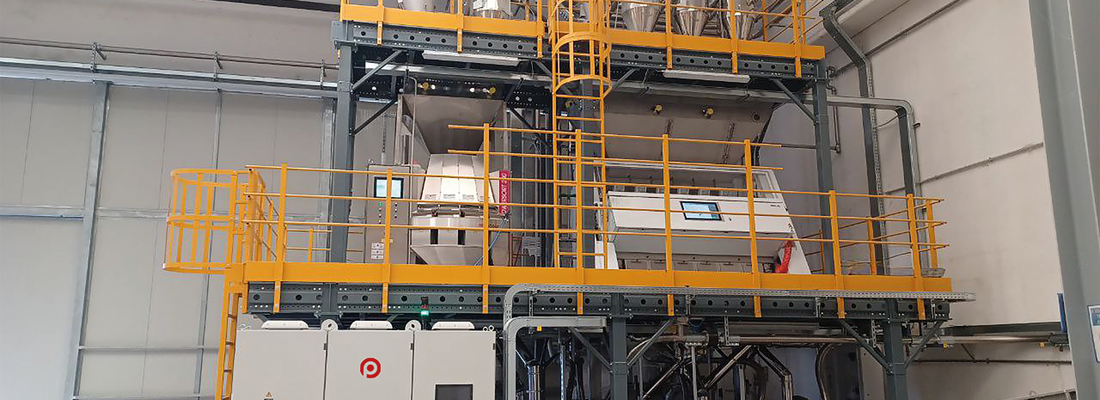
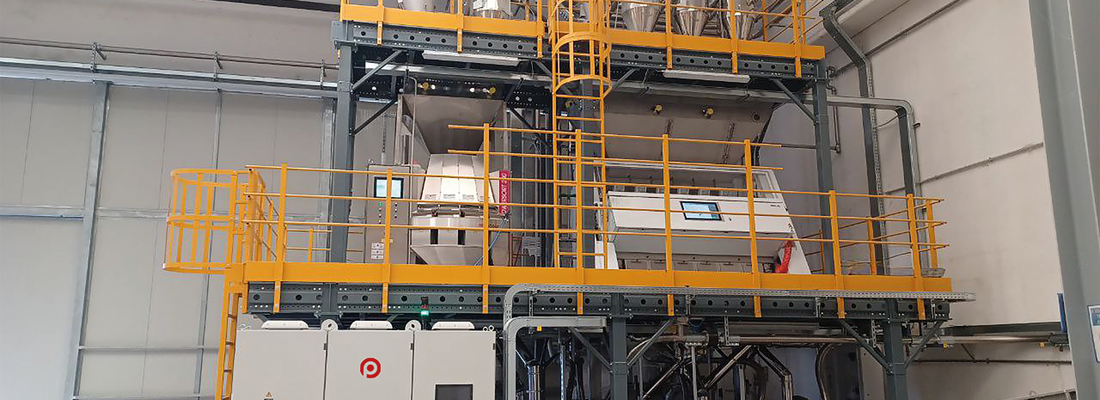
The PET Solutions system is a state-of-theart PET recycling plant designed to offer customers the capability to produce foodgrade PET regranulate. The process begins with washed post-consumer bottle flakes, which are subjected to a meticulously organized series of treatments, ultimately resulting in the production of exceptionally high-quality PET regranulate.
Main Process Components
First stage:
- Big bag emptying unit
- Vibrating sieve and dedusting system
- Flakes transportation and waste management from sorters
- Product storage units
- Gravimetric dosing system for recipe preparation
- Crystallization and dehumidification system
Second stage:
- Crystallinity increase system
- Deacetylation system
- Cooling system
- Finished product storage in big bags or silos
Detailed Overview of the Recycling Process
The recycling process starts with the management of PET flakes, which are introduced into the system via a big bag emptying unit or Silos. This step is crucial as it ensures a steady and uniform feed of material into the processing line, preventing disruptions and maintaining the efficiency of the subsequent stages. There are different solutions available like: a shaking system for those who want to recover the bag, and a cutting tool to empty the bag without the operator’s assistance.
Once the flakes are loaded, they are directed through a series of advanced sorters. These sorters employ cutting-edge optical and mechanical technologies to meticulously separate the flakes based on size, color, and material composition. This stage is essential for removing any residual contaminants, such as non-PET materials, metals, or colored flakes, with an accuracy of over 99.6%, ensuring that the resulting material is of the highest possible quality. There are various dedusting systems and storage options depending on the quality of incoming flakes.
Following the sorting process, the cleaned and sorted flakes are transferred (via thrust loading group or vacuum system) to storage silos (various types of silos are available, such as aluminum, flexible, and steel). These silos serve as temporary holding areas (to facilitate continuous processing without the need for 24/7 operator supervision), allowing the material to stabilize before entering the next phase of processing. The silos can hold up to 300 metric tons of PET flakes, facilitating a continuous and controlled flow of material into the downstream processes.
The next crucial step involves the crystallization process. Here, the flakes undergo thermal treatment in a crystallizer, where crystallinity is increased by up to 30-35%. The crystallization process is carefully controlled to increase the crystallinity, which is a critical parameter for ensuring the mechanical properties and quality of the regranulate. This stage also helps in reducing the moisture content of the material to below 50-100 parts per million (ppm), which is vital for preventing degradation during the subsequent processing stages.
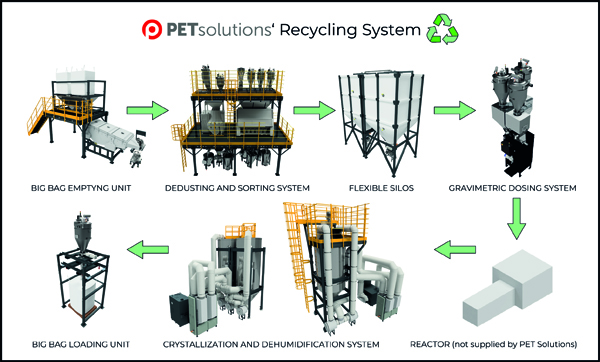
After crystallization, the material is fed into a reactor, where it undergoes further treatment. In the reactor, the PET is subjected to a solid-state polycondensation (SSP) process, which can increase the IV value to as high as 0.85-0.9 dl/g. The reactor is designed to maintain precise temperature and pressure conditions, optimizing the polymer chains and improving the overall material properties.
Finally, the treated PET is extruded into granules, which are then cooled and cut into uniform regranulate pellets. These pellets represent the final product, which is now ready for reuse in the production of new PET products, including food and beverage containers. The entire process is continuously monitored, with inline material supervisors ensuring that the intrinsic viscosity and other quality parameters meet the stringent requirements for food-grade materials. The product is finally stored in Big Bags or Silos equipped with weighing systems (for constant monitoring of material usage) and labeling of the final product.
Depending on the reactor used, the material at the end of the line may not meet the required standards for crystallinity and acetaldehyde levels. This is where Pet Solutions truly stands out. With advanced technology, Pet Solutions can take the hot, amorphous material at the end of the line and, through a dedicated crystallization and deacetylation process, achieve remarkable results: crystallinity levels of 35% and acetaldehyde levels of less than 1 ppm. This ensures that the material meets or exceeds industry standards, adding significant value to the production process.
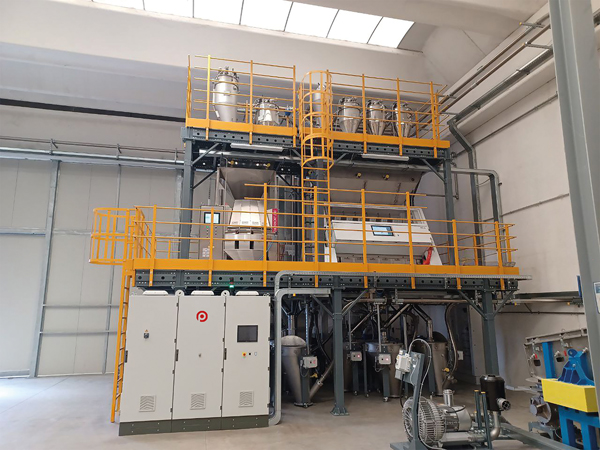
Advantages of the PET Solutions System
- Turnkey system covering all stages of the transformation process, from flakes to granules, in addition to providing the most modern dehumidification systems for rPET.
- Design and integration of the entire system with Sorter manufacturers and rPET producers.
- Supervision system and product traceability.
- Post reactor material treatment for crystallinity levels of 35% and acetaldehyde levels of less than 1 ppm.
The comPETence center provides your organisation with a dynamic, cost effective way to promote your products and services.
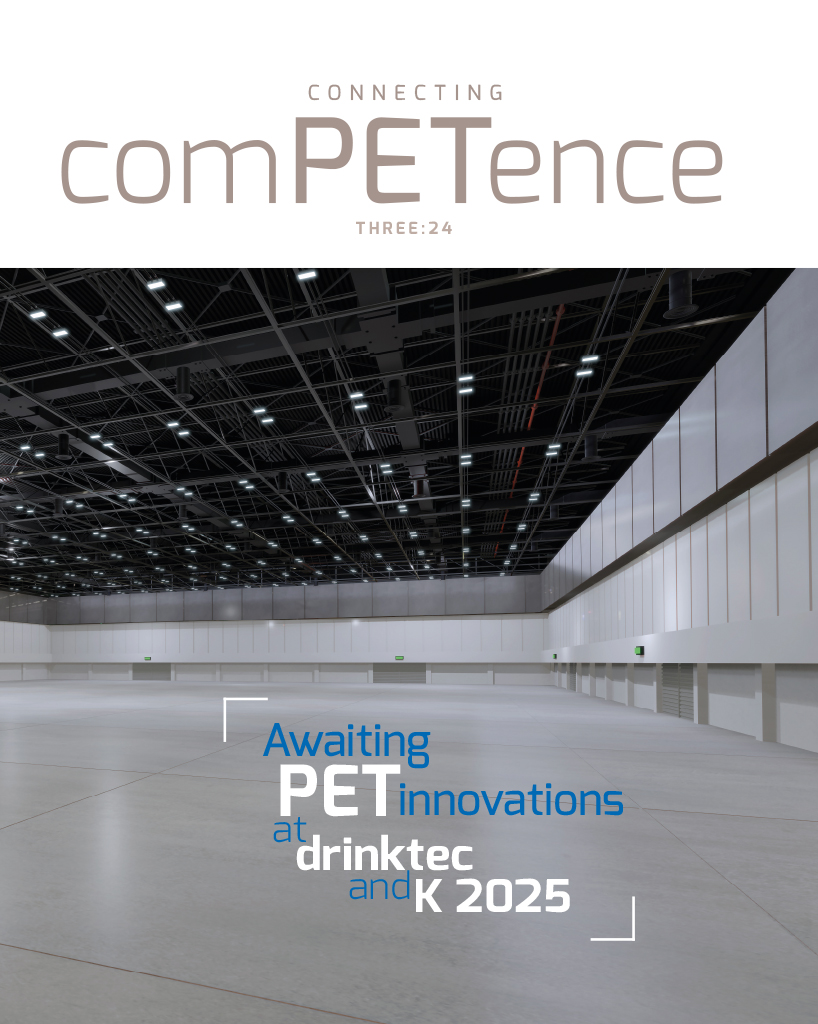
magazine
Find our premium articles, interviews, reports and more
in 3 issues in 2024.